Cetane Improver, 2-ethyl hexyl nitrate is an established technology with widespread use in diesel fuel blending. The boost to fuel cetane number is a reliable effect from moderate and economic dosages. The reactive free radicals produced as 2-ehn enters an engine’s cylinder, accelerate combustion and reduce ignition delay, increasing the fuel cetane number.
This powerful chemical effect enables refiners to profitably upgrade lower quality feeds.
The Cetane specification influences the refinery planning process from the selection of crude oil through to final diesel batch formulation. The capability of a refiner to make the best use of this technology can have a significant impact on refinery profitability.
Control of Cetane Improver Dosages
Production Planning
The planned blend formulation needs to be realistic for the base cetane number and the dosage of cetane improver calculated to move the result from the base to the fuel specification. Blender control systems can correct minor errors but need to make a ‘good start’ to be reliable. The component cetane will vary significantly for different feed sources and the formulation of blends to a cetane target requires reliable blending indices and rules.
The predicted blend cetane index (CI) is often used for the base cetane. The 2 and 4 variable Cetane Indices are correlations based on the density and distillation of the blend. The CI is useful, but not to be relied upon as the calculation assumes an even character across the distillation range. The calculation can be modified to be more accurate for specific blends types. Sampling components and checking the way they blend for cetane can help to establish blending rules.
Components of extreme character such as the highly paraffinic GTL or low boiling aromatic components tend to reduce the reliability of the cetane index calculations.
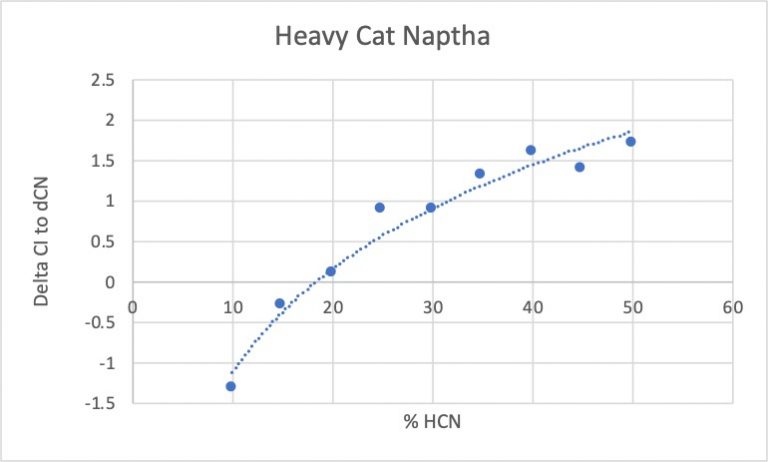
Example of an aromatic low boiling component causing the 4vCI calculation to predict higher values than the measured dCN. The chart shows the delta increase with HCN content
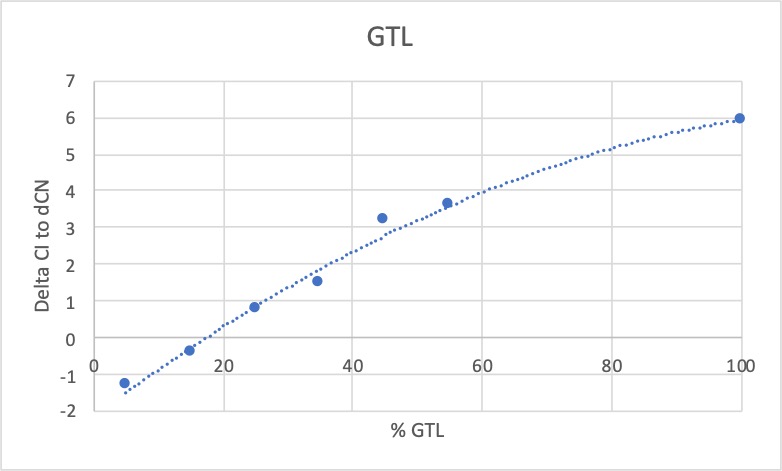
Example of a highly paraffinic mid-range boiling component causing the 4vCI calculation to predict higher values than the measured dCN. The chart shows the delta increase with GTL content.
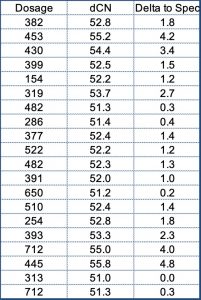
Snapshot of batch release results, which over a year’s blending achieved an average of 1.6 over specification with a standard deviation of 1.3. A significant proportion of the cetane additive is being wasted in aiming for a 51 specification.
The refinery was using cetane index calculated from on-line density and distillation for the base cetane, adding the estimated dosage part-way through the batch.
‘Splash Blending’ to a batch tank may allow time for rundown and tank analysis in the laboratory to help adjust additive dosages. The introduction of the IQT instrument has greatly improved the speed of analysis. Supporting laboratory studies can be run to measure and model the cetane improver effect and the non-linear shape of the response curve be taken into account when setting and adjusting dosages.
On-Line Controller & Cetane Improver Dosing
Advanced blenders are equipped with fast loop sampling and line analysers. These measure diesel properties as blends are being produced and control the blender in real time, optimizing the blend formulation and additive dosages. Density and distillation points are usually available to follow the cetane index, however as discussed, this can be unreliable for additive dosing. Direct measurement of the cetane number is the solution. Spectroscopic methods such as N IR are available, but require a continuous calibration support to maintain accuracy. A new instrument is the Icon systems on-line cetane analyser. This instrument was recently developed in a major project to solve the problem of accurate blending to the specification and also more efficient use of the additive.